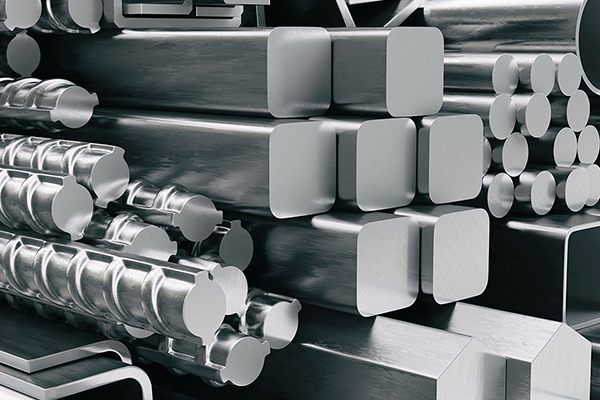
金属切削
加工过程中刀具与工件之间相互作用和各自的变化规律是一门学科。在设计机床和刀具﹑制订机器零件的切削工艺及其定额﹑合理地使用刀具和机床以及控制切削过程时﹐都要利用金属切削原理的研究成果﹐使机器零件的加工达到经济﹑优质和高效率的目的。下面就简单介绍下常规的切削工艺改进方案有哪些:
一、切削刀具的选用
通常情况下,工件的精加工与粗加工选用刀具有一定区别。在粗加工中由于不必考虑精度及质量问题,可以最大限度高效切除金属材料,因此可以选择大直径刀具,减少走刀次数,缩短走刀时间。另外,在粗加工中尽量选择密齿刀具替代疏齿刀具,可以增加每转进给量,在相同的转速下切削速度可以得到增加。在精加工中,除了考虑材料高效去除的问题,还应充分考虑薄壁构件在切削中受力变形控制问题。
对于不同材质的工件,选用的刀具也存在差异。铝合金材料的切削对刀具材料要求不高,一般采用硬质合金铣刀即可,涂层可使用无涂层或金刚石涂层。航天铝合金薄壁件精加工宜选用K系列硬质合金刀具。
二、刀具角度的调整
刀具前角太小会增大切削变形和摩擦力,前刀面磨损加大降低刀具使用寿命,而刀具后角的选取会影响刀具刚度。为了减少刀具和工件之间的摩擦,后角一定要选得大一些,必要时可采用双倒棱后角,在增大后角的同时保证刀具刚度。刃倾角影响了切屑流出的方向和各切削分力的大小,在铝合金切削时宜选用较大的刃倾角。
三、切削油的选用
切削油在切削工艺中在刀具和工件起到了承接的作用,性能良好的切削油产品具有良好的极压抗磨性能,防止刀具与工件直接接触,降低切削工艺的难度,并能有效的保护刀具并大幅度提高加工效率。
根据实际工艺工况选用专用切削油,可以解决由于油品问题导致的工件精度差,刀具磨损快,机台生锈且加工时烟雾大等问题,减少企业的设备维护成本。
四、走刀轨迹
提速增效中一个较为有效的方法就是优化走刀轨迹,在高速切削时要保证刀位路径的方向性,即刀具轨迹尽可能简化,少转折点,路径尽量平滑,减少急速转向;应减少空走刀时间,尽可能增加切削时间在整个工件中的比例;应尽量采用回路切削,通过不中断切削过程和刀具路径,减少刀具的切入和切出次数,获得稳定、高效、高精度的切削过程。
在斜面加工时,若采用横向水平走刀,每一段走刀距离都很短,在切削过程中主轴需要频繁换向,切削稳定性差,且由于切削的是斜面,,不利于切削速度的提升。因此,针对此类斜面加工,走刀轨迹尽量安排为平行于最长斜边,不但走刀轨迹最长、换向次数最少,即使在高速切削下亦可减小刀具损伤。
五、切削参数
在粗加工时,一般可选择大进给量与适当大的切削深度并配以中等切削速度的“大功率”高效切削,更能达到高材料切除率,从而极大提高生产效率。而对于精加工来说,只有提高转速和增大齿数是可行的,而增大每齿进给量可能会降低表面精度,产生残余应力导致变形。所以往往通过高切削速度、低每齿进给量的“轻切快切”来保证生产效率的提高和产品的精度及表面质量。
针对不同工艺参数下的机床主轴功率与扭矩需求,进行了仿真分析运算,获取机床主轴能够很好地满足产品高速加工工艺需求的主轴转速、每齿进给量和切削深度等要素的可选范围,为切削试验参数选择提供指导性建议。
随着工业
技术水平的不断提高,纳米技术、网络技术、复合材料应用、智能机器人等关键技术也日趁成熟,金属加工行业的也将面临革新。如何提高车床加工工艺以满足日益增长的企业要求将成为行业的下一个课题。
免责声明: 1、文章部分文字与图片来源网络,如有问题请及时联系我们。 2、因编辑需要,文字和图片之间亦无必然联系,仅供参考。涉及转载的所有文章、图片、音频视频文件 等资料,版权归版权所有人所有。 3、本文章内容如无意中侵犯了媒体或个人的知识产权,请联系我们立即删除,联系方式:请邮件发送至 CNC1698@l63.com