铝合金零件
精密挤压_铝合金零件精密挤压技术
大家好!今天让小编来大家介绍下关于铝合金零件精密挤压_铝合金零件精密挤压技术的问题,以下是小编对此问题的归纳整理,来看看吧。
文章目录列表:
- 如何预防6063和6061铝型材在挤压过程中拖黑和夹渣
- 铝合金挤压机操作教程
- 6082铝合金挤压铝型材生产工艺研究
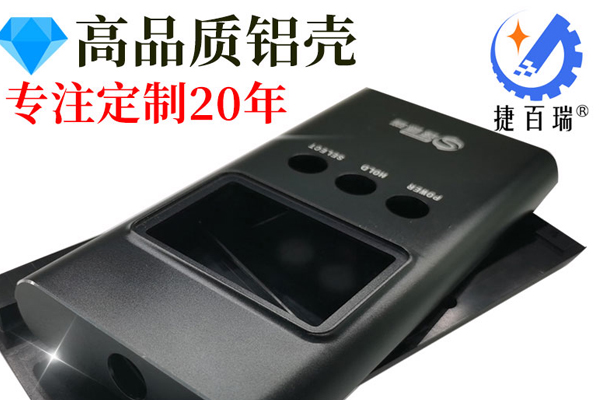
如何预防6063和6061铝型材在挤压过程中拖黑和夹渣
为了解决6063和6061铝型材有关拖黑、夹渣的缺陷问题,减少报废量,提高成品率。通过长期的跟踪,对预防6063和6061铝型材拖黑、夹渣提出以下三个方法来解决:
1、生产工艺控制
1)剪完棒要用风管吹干净铝棒上的尘土,减少带入的灰土等,减少拖黑、夹渣的来源;2)压余厚度要留够,太薄的压余会导铝棒死区卷入型材尾端,造成拖黑、夹渣;
3)挤压速度要进行有效的控制,特别是末端要进行减速处理,防止紊流卷入表皮杂质;4)每生产一段时间要进行清缸;
2、设备、装置的调整
1)如挤压杆没有对中,挤压杆运动中磨损料胆,会造成料胆大肚、变形等缺陷;
2)模座中心位,上、下、左、右要对中,严禁移动模座进行生产,上下不对中的,要联系机修进行维修;
3)压饼大小要进行定期检测并换新,对于卷边的挤压饼,也会造成拖黑、夹渣等报废;4)料胆长期使用,出现大肚等变形,也会造成批量报废,此种报废在生产中出现非常多,需要引起重视,新料胆一定将胆内的脏物去除并对内胆进行抛光后才能上机安装。
3、模具设计、生产计划的调整
1)对于平面模,如有需要加装导流板进行导流,这样做缩小了进料口,钳制住死区;2)料胆口必须充分包围模具分流孔,班长要对每装一套模具进行对比,如有分流孔过大的现象,不能上机生产,要转大机生产;
3)生产下计划时,要根据模具部开模的原始机台(同棒径的可以通用)下计划,不要出现小棒生产大棒机台的模具。
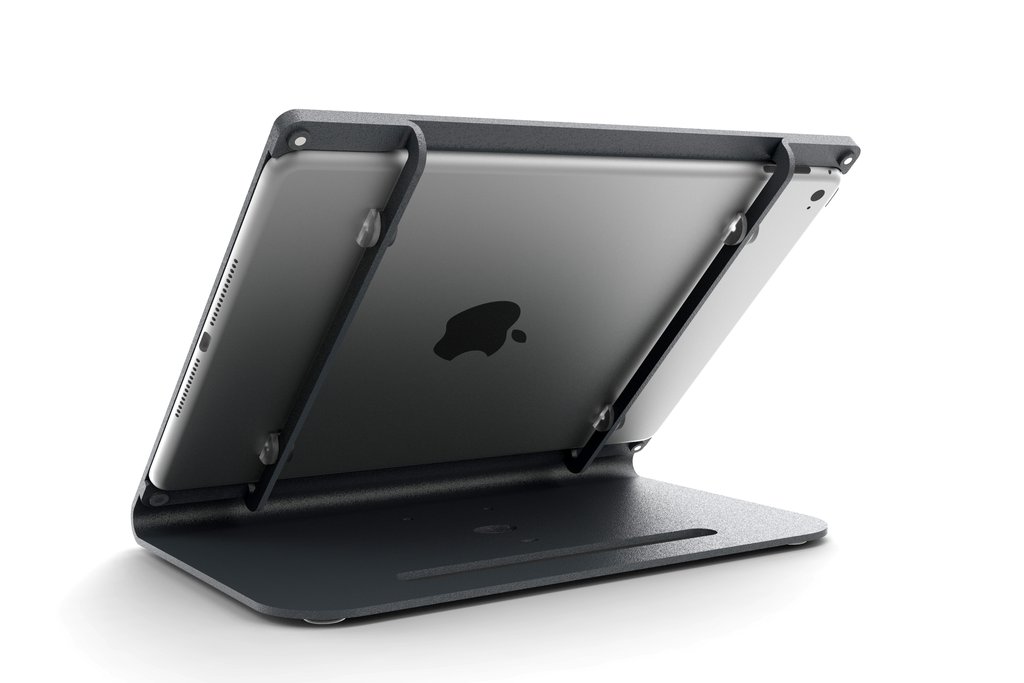
铝合金挤压机操作教程
熔炼时,装入炉料的顺序和方法不仅关系到熔炼的时间、金属的烧损、热能消耗,还会影响到金属熔体的质量和炉子的使用寿命。装料的原则有:
1、装炉料顺序应合理。正确的装料要根据所加入炉料性质与状态而定,而且还应考虑到最快的熔化速度,最少的烧损以及准确的化学成分控制。
装料时,先装小块或薄片废料,铝锭和大块料装在中间,最后装中间合金。熔点易氧化的中间合金装在中下层。所装入的炉料应当在熔池中均匀分布,防止偏重。
小块或薄板料装在熔池下层,这样可减少烧损,同时还可以保护炉体免受大块料的直接冲击而损坏。中间合金有的熔点高,如AL-NI和AL-MN合金的熔点为750-800℃,装在上层,由于炉内上部温度高容易熔化,也有充分的时间扩散;使中间合金分布均匀,则有利于熔体的成分控制。
炉料装平,各处熔化速度相差不多这样可以防止偏重时造成的局部金属过热。
炉料应进量一次入炉,二次或多次加料会增加非金属夹杂物及含气量。
2、对于质量要求高的产品(包括锻件、模锻件、空心大梁和大梁型材等)的炉料除上述的装料要求外,在装料前必须向熔池内撒20-30kg粉状熔剂,在装炉过程中对炉料要分层撒粉状熔剂,这样可提高炉体的纯洁度,也可以减少损耗。
3、电炉装料时,应注意炉料最高点距电阻丝的距离不得少于100mm,否则容易引起短路。
熔化
炉料装完后即可升温。熔化是从固态转变为液态的过程。这一过程的好坏,对产品质量有决定性的影响。
A、覆盖
熔化过程中随着炉料温度的升高,特别是当炉料开始熔化后,金属外层表面所覆盖的氧化膜很容易破裂,将逐渐失去保护作用。气体在这时候很容易侵入,造成内部金属的进一步氧化。并且已熔化的液体或液流要向炉底流动,当液滴或液流进入底部汇集起来时,其表面的氧化膜就会混入熔体中。所以为了防止金属进一步氧化和减少进入熔体的氧化膜,在炉料软化下塌时,应适当向金属表面撒上一层粉状熔剂覆盖,其用量见表。这样也可以减少熔化过程中的金属吸气。
B、加铜、加锌
当炉料熔化一部分后,即可向液体中均匀加入锌锭或铜板,以熔池中的熔体刚好能淹没住锌锭和铜板为宜。
这时应强调的是,铜板的熔点为1083℃,在铝合金熔炼温度范围内,铜是溶解在铝合金熔体中。因此,铜板如果加得过早,熔体未能将其盖住,这样将增加铜板的烧损;反之如果加得过晚,铜板来不及溶解和扩散,将延长熔化时间,影响合金的化学成分控制。
电炉熔炼时,应尽量避免更换电阻丝带,以防脏物落入熔体中,污染金属。
C、搅动熔体
熔化过程中应注意防止熔体过热,特别是天然气炉(或煤气炉)熔炼时炉膛温度高达1200℃,在这样高的温度下容易产生局部过热。为此当炉料熔化之后,应适当搅动熔体,以使熔池里各处温度均匀一致,同时也利于加速熔化。
扒渣与搅拌
当炉料在熔池里已充分熔化,并且熔体温度达到熔炼温度时,即可扒除熔体表面漂浮的大量氧化渣。
A、扒渣
扒渣前应先向熔体上均匀撒入粉状熔剂,以使渣与金属分离,有利于扒渣,可以少带出金属。扒渣要求平稳,防止渣卷入熔体内。扒渣要彻底,因浮渣的存在会增加熔体的含气量,并弄脏金属。
B、加镁加铍
扒渣后便可向熔体内加入镁锭,同时要用2号粉状熔剂进行覆盖,以防镁的烧损。
对于高镁铝合金为防止镁的烧损,并且改变熔体及铸锭表面氧化膜的性质,在加镁后须向熔体内加入少量(0.001%-0.004%)的铍。铍一般以Al-BeF4与2号粉状熔剂按1:1混合加入,加入后应进行充分搅拌。
Na BeF +Al→2NaF+AlF +Be
为防止铍的中毒,在加铍操作时应戴好口罩。另外,加铍后扒也的渣滓应堆积在专门的堆放场地或作专门处理。
C、搅拌
在取样之前,调整化学成分之后,都应当及时进行搅拌。其目的在于使合金成分均匀分布和熔体内温度趋于一致。这看起来似乎是一种极其简单的操作,但是在工艺过程中是很重要的工序。因为,一些密度较大的合金元素容易沉底,另外合金元素的加入不可能绝对均匀,这就造成了熔体上下层之间,炉内各区域之间合金元素的分布不均匀。如果搅拌不彻底(没有保证足够长的时间和消灭死角),容易造成熔体化学成分不均匀。
搅拌应当平稳进行,不应激起太大的波浪,以防氧化膜卷入熔体中。
调整成分
在熔炼过程中,由于各种原因都可能会使合金成分发生改变,这种改变可能使熔体的真实成分与配料计算值发生较大的偏差。因而需在炉料熔化后,取样进行快速分析,以便根据分析结果是否需要调整成分。
A、取样
熔体经充分搅拌后,即应取样进行炉前快速分析,分析化学成分是否符合标准要求。取样时的炉内熔体温度应不低于熔炼温度中限。
快速分析试样的取样部位要有代表性,开然气炉(或煤气炉)在两个炉门中心部位各取一组试样,电炉在二分之一熔体的中心部位取两组试样。取样前试样勺要进行预热,对于高纯铝及铝合金,这了防止试样勺污染,取样应采用不锈钢试样勺并涂上涂料。
B、成分调整
当快速分析结果和合金成分要求不相符时,就应调整成分——冲淡或补料。
(1)补料。快速分析结果低于合金化学成分要求时需要补料。为了使补料准确,应按下列原则进行计算:
1)先算量少者后算量多者;
2)先算杂质后算合金元素;
3)先算低成分的中间合金,后算高成分的中间合金;
4)最后算新金属
一般可按下式近似地计算出所需补加的料量,然后予以核算,算式如下:
X=
式中X——所需补加的料量,kg;
Q——熔体总量(即投料量),kg;
a——某成分的要求含量,%;
b——该成分的分析量,%;
c c ——分别为其它金属或中间合金的加入量,kg;
d——补料用中间合金中该成分的含量(如果是加纯金属,则d=100),%。
(2)冲淡。
快速分析结果高于化学成分的国家标准、交货标准等的上限时就需冲淡。
在冲淡时高于化学成分标准的合金元素要冲至低于标准要求的该合金元素含量上限。
我国的铝
加工厂根据历年来的生产实践,对于铝合金都制定了厂内标准,以便使这些合金获得良好的铸造性能和力学性能。为此,在冲淡时一般都冲至接近或低于该元素的厂内化学成分标准上限所需的化学成分。
在冲淡时一般按照下式计算出所需的冲淡量。
X=Q(b-a)/a
式中b——某成分的分析量,%;
a——该成分的(厂内)标准上限的要求含量,%;
Q——熔体总量,kg;
X——所需的冲淡量,kg;
C 调整成分时应注意的事项
(1)试样用元代表性。试样无代表性是加为,某些元素密度较大,溶解扩散速度慢,或易于偏析分层。故取样前应充分搅拌,以均匀其成分,由于反射炉熔池表面温度高,炉底温度低,没有对流传热作用,取样前要多次搅拌,每次搅拌时间不得少于5min。
(2)取样部位和操作方法要合理。由于反射炉熔池大而深,尽管取样前进行多次搅拌,熔池内各部位的成分仍然有一定的偏差,因此,试样应在熔池中部最深部位的二分之一处取出。
取样前应将试样模充分加热干燥,取样时操作方法正确,使试样符合要求,否则试样有气孔、夹渣或不符合要求,都会给快速分析带来一定的误差。
(3)取样时温度要适当。某些密度大的元素,它的溶解扩散速度随着温度的升高而加快。如果取样前熔体温度较低,虽然经过多次搅拌,其溶解扩散速度仍然很慢,此时取出的试样仍然无代表性,因此取样前应控制熔体温度适当高些。
(4)补料和冲淡时一般都用中间合金,熔点较高和较难熔化的新金属料,应予避免。
(5)补料量和冲淡量在保证合金元素要求的前提下应越少越好。且冲淡时应考虑熔炼炉的容量和是否便于冲淡的有关操作。
(6)如果在冲淡量较大的情况下,还应补入其它合金元素,应使这些合金元素的含量不低于相应的标准或要求。
精炼
工业生产的铝合金绝大多数在熔炼炉不再设气体精炼钢过程,而主要靠静置炉精炼和在线熔体净化处理,便有的铝
加工厂仍还设有熔炼炉精炼,其目的是为了提高熔体的纯净度。这些精炼方法可分为两类:即气体精炼法和熔剂精炼法。
出炉
当熔体经过精炼处理,并扒出表面浮渣后,待温度合适时,即可将金属熔体输注到静置炉,以便准备铸造。
清炉
清炉就是将炉内残存的结渣彻底清出炉外。每当金属出炉后,都要进行一次清炉。当合金转换,普通制品连续生产5-15炉,特殊制品每生产一炉,一般就要进行大清炉。大清炉时,应先均匀向炉内撒入一层粉状熔剂,并将炉膛温度升至800℃以上,然后用三角铲将炉内各处残存的结渣彻底清除。更多铝合金相关信息请关注上海有色网( http://www.smm.cn)
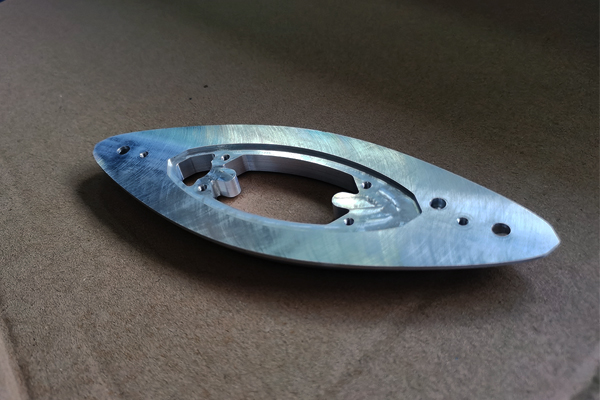
6082铝合金挤压铝型材生产工艺研究
1.前言
6082铝合金属于Al - Mg - Si系热处理可强化的铝合金,具有中等强度和良好的焊接性能和耐腐蚀性,主要被用于交通运输和结构工程上,如桥梁、起重机、屋顶构架、交通车和运输船等。
本文对6082铝合金应用于挤压型材生产进行了试验研究,以确定合适的熔铸和挤压工艺制度。
2.熔铸工艺
2.1化学成分
GB/T3190 -1996中6082铝合金化学成分见表1。
6082铝合金成分具有两个主要特点:第一,含有适量的Mn和Cr;第二,Mg、Si含量相对较高。其中,Mn、Cr等合金元素可阻碍挤压时和挤压后发生再结晶或再结晶晶粒长大,细化晶粒。但(Mn + Cr) 总量过高可能形成分别含Mn、Cr的粗大第二相,削弱Mg 2 Si相的沉淀强化效果,抵消其阻碍再结晶和细化晶粒的作用。同时,Mn、Cr元素会增大6082铝合金的淬火敏感性。且易在α(Al)相中产生严重的晶内偏析,造成挤压制品粗晶组织,降低型材氧化着色效果。对于Mg、Si成分,6082铝合金在Mg 2 Si强化的同时,通过增加适量过剩Si来促进强化。
因此,重点对Mn的含量进行试验确定:以Mn含量为0.6% ~0.65%及0.9% ~0.95%进行对比。发现Mn含量偏上限时,制品尾部粗晶组织较多,且力学性能偏低,所以对比确定Mn含量的优化范围为0. 6% ~0.65%。Cr的含量宜控制在0.15%以下,(Mn + Cr)总量控制在0.70% ~0.80%范围内。Mg 2 Si含量宜控制在1.5% ~ 1.6%,过剩Si含量控制在0.3%左右。
6082铝合金的实际成分控制范围见表2。
2.3工艺控制
由于6082铝合金最大的特点是含难熔金属Mn,Mn的适量存在易引起晶内偏析及固液区塑性降低,导致抗裂能力不足,故熔铸工艺主要需注意三点:第一,熔炼应注意控制温度在740 760℃间并搅拌均匀,保证金属完全熔化、温度准确、成分均匀。第二,铸造应考虑金属Mn增大了合金的粘度,使其流动性下降,影响了合金铸造性能。铸造速度要适当降低,控制在80 100mm/min范围内。第三,加大冷却强度,加快冷却速度,以利于消除晶内偏析现象。控制一次冷却强度,加大二次冷却强度以减少铸造时产生的应力集中,避免产生铸锭裂纹缺陷。冷却水压应控制在0. 1 ~0.3MPa范围内。
3.均匀化退火
6082铝合金变形抗力大,力学性能指标偏高。通过均匀化处理工艺改善合金组织,达到三个主要效果:充分固溶解Mg 2 Si相;消除晶内偏析;β(Al 9 Fe 2 Si 2 )相向α(Al 12 Fe 3 Si 2 )相转变,并细化含铁相粒子。
由于合金中Mn的存在可降低转变温度、缩短转变时间,且为保持合金挤压性能和挤压效应,采用中温均化工艺,即均匀化温度555 ~565℃;保温时间6h;冷却速度≥200℃/h。
4.挤压工艺
4.1铸锭加热方式
铸锭加热采用工频感应加热,这种加热方式的特点是加热时间短,在3min内即可达到500℃左右;温度控制准确,误差不超过±3℃。如果用电阻炉缓慢加热,将会导致Mg 2 Si相析出,影响强化效果。
4.2挤压
综合考虑6082铝合金的主要特点,结合实践生产制订挤压工艺如下:
(1)、6082合金变形抗力大,所以铸锭加热温度应偏上限(480 ~500℃)。
(2)、模具温度取460℃为宜,挤压筒温度为440 ~500℃。
(3)、挤压速度控制在7~11m/min的范围内;
(4)、要使合金主要强化相Mg 2 Si完全固溶,须保证淬火温度在500℃以上,因此型材挤压出口温度应控制在500 ~530℃范围内;
(5)、6082合金淬火敏感性高,要求淬火冷却强度大、冷却速度快,制品出前梁后必须立即进行在线淬火。对于壁厚2.5mm以下的型材可考虑用强风冷却淬火;壁厚2.5mm以上的型材必须用水雾淬火处理,须使温度迅速降到50℃以下。
(6)、6082铝合金型材拉伸矫直,应将拉伸率控制在1.0% ~2.0%范围内。挤压工艺参数见表3。
5.时效制度
时效是型材达到规定力学性能的最后一个环节,合理的时效制度既要保证产品的性能,又要考虑生产效率及生产成本。结合试验研究,6082型材最佳时效制度定为:时效温度170 ~ 180℃,保温时间8h,时效前型材的停放时间不超过8h。
6.结论
根据6082铝合金型材的特点和性能要求,上述工艺是比较合理的。在熔铸工艺中,6082铝合金成分控制重点在于Mn和Cr含量范围。Mn含量优化控制范围为0.6%~0. 65%,Cr的含量宜控制在0. 15% 以下,(Mn + Cr)总量控制在0.70% ~0.80% 范围内。Mg 2 Si含量宜控制在1.5% ~ 1.6%,过剩 Si含量控制在0.3%左右。在挤压工艺中,挤压出口温度和淬火效果控制则是保证产品性能的关键,应保证淬火温度在500℃以上,型材挤压出口温度应控制在500 ~530℃,淬火力求强度大、速度快。
以上就是小编对于铝合金零件精密挤压_铝合金零件精密挤压技术问题和相关问题的解答了,铝合金零件精密挤压_铝合金零件精密挤压技术的问题希望对你有用!
免责声明: 1、文章部分文字与图片来源网络,如有问题请及时联系我们。 2、因编辑需要,文字和图片之间亦无必然联系,仅供参考。涉及转载的所有文章、图片、音频视频文件 等资料,版权归版权所有人所有。 3、本文章内容如无意中侵犯了媒体或个人的知识产权,请联系我们立即删除,联系方式:请邮件发送至 cnc1698@l63.com