铝合金零件铸造过程_铝合金零件铸造过程图片
大家好!今天让小编来大家介绍下关于铝合金零件铸造过程_铝合金零件铸造过程图片的问题,以下是小编对此问题的归纳整理,来看看吧。
文章目录列表:
- 铸造工艺流程
- 铝合金是如何制作出来的?
- 铸造工艺流程

铸造工艺流程
砂型铸造的主要流程有:
模具生产部分:按照图纸要求制作制作模具,一般单件生产可以用木模、批量生产可以制作塑料模、金属模,大批量铸件可以制作模板。
2.混砂阶段:按照砂型制造的要求及铸件的种类不同,配制合格的型砂,以供造型所用。
3.造型(制芯)阶段:包括了造型(用型砂形成铸件的形腔)、制芯(形成铸件的内部形状)、配模(把坭芯放入型腔里面,把上下砂箱合好)。造型是铸造中的关键环节。
4.熔炼阶段:按照所需要的金属成份配好化学成份,选择合适的熔化炉熔化合金材料,形成合格的液态金属液(包括成份合格,温度合格)
5.浇注阶段:把合格的融熔金属注入配好模的砂箱里。浇注阶段危险性比较大,要特种注意。
6.清理阶段:浇注后等融熔金属凝固后,把型砂清除掉,打掉浇口等附设件,就形成了所需要的铸件了。
扩展资料
总体概述
制造砂型的基本原材料是铸造砂和型砂粘结剂。最常用的铸造砂是硅质砂。硅砂的高温性能不能满足使用要求时则使用锆英砂、铬铁矿砂、刚玉砂等特种砂。为使制成的砂型和型芯具有一定的强度,在搬运、合型及浇注液态金属时不致变形或损坏,一般要在铸造中加入型砂粘结剂,将松散的砂粒粘结起来成为型砂。应用最广的型砂粘结剂是粘土,也可采用各种干性油或半干性油、水溶性硅酸盐或磷酸盐和各种合成树脂作型砂粘结剂。砂型铸造中所用的外砂型按型砂所用的粘结剂及其建立强度的方式不同分为粘土湿砂型、粘土干砂型和化学硬化砂型3种。
粘土湿砂
以粘土和适量的水为型砂的主要粘结剂,制成砂型后直接在湿态下合型和浇注。湿型铸造历史悠久,应用较广。湿型砂的强度取决于粘土和水按一定比例混合而成的粘土浆。型砂一经混好即具有一定的强度,经舂实制成砂型后,即可满足合型和浇注的要求。因此型砂中的粘土量和水分是十分重要的工艺因素。
以型砂和芯砂为造型材料制成铸型,液态金属在重力下充填铸型来生产铸件的铸造方法。钢、铁和大多数有色合金铸件都可用砂型铸造方法获得。由于砂型铸造所用的造型材料价廉易得,铸型制造简便,对铸件的单件生产、成批生产和大量生产均能适应,长期以来,一直是铸造生产中的基本工艺。
砂型铸造所用铸型一般由外砂型和型芯组合而成。为了提高铸件的表面质量,常在砂型和型芯表面刷一层涂料。涂料的主要成分是耐火度高、高温化学稳定性好的粉状材料和粘结剂,另外还加有便于施涂的载体(水或其他溶剂)和各种附加物。
粘土湿砂型铸造的优点是:①粘土的资源丰富、价格便宜。②使用过的粘土湿砂经适当的砂处理后,绝大部分均可回收再用。③制造铸型的周期短、工效高。④混好的型砂可使用的时间长。⑤砂型舂实以后仍可容受少量变形而不致破坏,对拔模和下芯都非常有利。缺点是:①混砂时要将粘稠的粘土浆涂布在砂粒表面上,需要使用有搓揉作用的高功率混砂设备,否则不可能得到质量良好的型砂。②由于型砂混好后即具有相当高的强度,造型时型砂不易流动,难以舂实,手工造型时既费力又需一定的技巧,用机器造型时则设备复杂而庞大。③铸型的刚度不高,铸件的尺寸精度较差。④铸件易于产生冲砂、夹砂、气孔等缺陷。
粘土干砂型制造这种砂型用的型砂湿态水分略高于湿型用的型砂。
粘土砂芯用粘土砂制造的简单的型芯。
参考资料来源:百度百科:砂型铸造
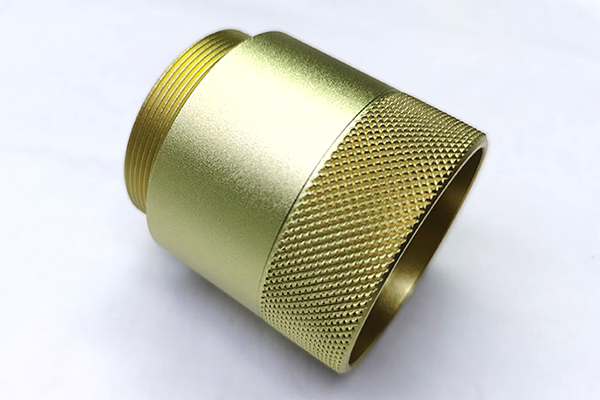
铝合金是如何制作出来的?
铝合金中铝作为基体含量非常高随便举个例子:Al-Cu-Mg系硬铝合金中的LY1,铜含量为2.2%-3.0%,镁含量0.2%-0.5%,其余均为铝。在整个过程中也并不是很长时间,不会让重的元素完全沉淀到铝液的底部;同时工业上有很多搅拌方式使得这些元素尽可能的均匀分布。
再一个你的问题有点问题,你应该是想问铝合金是怎么样铸造出来,而锻造是机械
加工的一种方式,铝合金锻造是指固态情况下对铝合金进行加工。
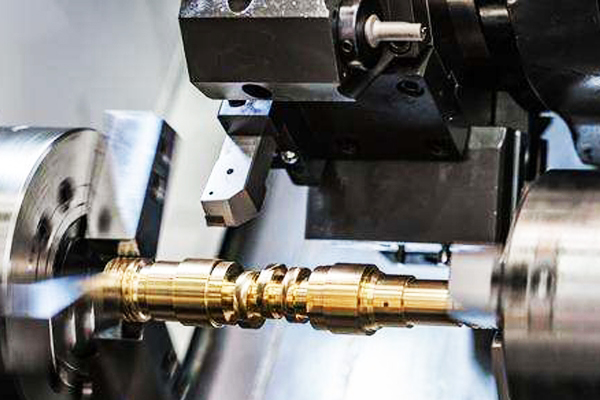
铸造工艺流程
铸造生产的工艺流程
铸造生产是一个复杂的多工序组合的工艺过程,它包括以下主要工序:
1)生产工艺准备,根据要生产的零件图、生产批量和交货期限,制定生产工艺方案和工艺文
件,绘制铸造工艺图;
2)生产准备,包括准备熔化用材料、造型制芯用材料和模样、芯盒、砂箱等工艺装备;
3)造型与制芯;
4)熔化与浇注;
成形原理
铸造生产是将金属加热熔化,使其具有流动性,然后浇入到具有一定形状的铸型型腔中,在
重力或外力(压力、离心力、电磁力等)的作用下充满型腔,冷却并凝固成铸件(或零件)
的一种金属成形方法。
图 1 铸造成形过程
铸件一般作为毛坯经切削加工成为零件。但也有许多铸件无需切削加工就能满足零件的设计
精度和表面粗糙度要求,直接作为零件使用。
型砂的性能及组成
1、 型砂的性能
型砂(含芯砂)的主要性能要求有强度、透气性、耐火度、退让性、流动性、紧实率和溃散
性等。
2、 型砂的组成
型砂由原砂、粘接剂和附加物组成。铸造用原砂要求含泥量少、颗粒均匀、形状为圆形和多
角形的海砂、河砂或山砂等。铸造用粘接剂有粘土(普通粘土和膨润土)、水玻璃砂、树脂、
合脂油和植物油等,分别称为粘土砂,水玻璃砂、树脂砂、合脂油砂和植物油砂等。为了进
一步提高型(芯)砂的某些性能,往往要在型(芯)砂中加入一些附加物,如煤份、锯末、
纸浆等。型砂结构,如图 2 所示。
图 2 型砂结构示意图
工艺特点
铸造是生产零件毛坯的主要方法之一,尤其对于有些脆性金属或合金材料(如各种铸铁件、
有色合金铸件等)的零件毛坯,铸造几乎是唯一的加工方法。与其它加工方法相比,铸造工
艺具有以下特点:
1)铸件可以不受金属材料、尺寸大小和重量的限制。铸件材料可以是各种铸铁、铸钢、铝合
金、铜合金、镁合金、钛合金、锌合金和各种特殊合金材料;铸件可以小至几克,大到数百
吨;铸件壁厚可以从 0.5 毫米到 1 米左右;铸件长度可以从几毫米到十几米。
2)铸造可以生产各种形状复杂的毛坯,特别适用于生产具有复杂内腔的零件毛坯,如各种箱
体、缸体、叶片、叶轮等。
3)铸件的形状和大小可以与零件很接近,既节约金属材料,又省切削加工工时。
4)铸件一般使用的原材料来源广、铸件成本低。
5)铸造工艺灵活,生产率高,既可以手工生产,也可以机械化生产。
铸件的手工造型
手工造型的主要方法
砂型铸造分为手工造型(制芯)和机器造型(制芯)。手工造型是指造型和制芯的主要工作均
由手工完成;机器造型是指主要的造型工作,包括填砂、紧实、起模、合箱等由造型机完成。
泊头铸造工量具友介绍手工造型的主要方法:
手工造型因其操作灵活、适应性强,工艺装备简单,无需造型设备等特点,被广泛应用于单
件小批量生产。但手工造型生产率低,劳动强度较大。手工造型的方法很多,常用的有以下
几种:
1. 整模造型
对于形状简单,端部为平面且又是最大截面的铸件应采用整模造型。整模造型操作简便,造
型时整个模样全部置于一个砂箱内,不会出现错箱缺陷。整模造型适用于形状简单、最大截
面在端部的铸件,如齿轮坯、轴承座、罩、壳等(图 2)。
图 整模造型
2.分模造型
当铸件的最大截面不在铸件的端部时,为了便于造型和起模,模样要分成两半或几部分,这
种造型称为分模造型。当铸件的最大截面在铸件的中间时,应采用两箱分模造型(图 3),模
样从最大截面处分为两半部分(用销钉定位)。造型时模样分别置于上、下砂箱中,分模面(模
样与模样间的接合面)与分型面(砂型与砂型间的接合面)位置相重合。两箱分模造型广泛
用于形状比较复杂的铸件生产,如水管、轴套、阀体等有孔铸件。
图 3 套管的分模两箱造型过程
铸件形状为两端截面大、中间截面小,如带轮、槽轮、车床四方刀架等,为保证顺利起模,
应采用三箱分模造型(图 4)。此时分模面应选在模样的最小截面处,而分型面仍选在铸件两
端的最大截面处,由于三箱造型有两个分型面,降低了铸件高度方向的尺寸精度,增加了分
型面处飞边毛刺的清整工作量,操作较复杂,生产率较低,不适用于机器造型,因此,三箱
造型仅用于形状复杂、不能用两箱造型的铸件生产。
图 4 三箱分模造型举例
3.活块模造型
铸件上妨碍起模的部分(如凸台、筋条等)做成活块,用销子或燕尾结构使活块与模样主体
形成可拆连接。起模时先取出模样主体,活块模仍留在铸型中,起模后再从侧面取出活块的
造型方法称为活块模造型(图 5)。活块模造型主要用于带有突出部分而妨碍起模的铸件、单
件小批量、手工造型的场合。如果这类铸件批量大,需要机器造型时,可以用砂芯形成妨碍
起模的那部分轮廓。
图 5 角铁的活块模造型工艺过程
4.挖砂造型
当铸件的外部轮廓为曲面(如手轮等)其最大截面不在端部,且模样又不宜分成两半时,应
将模样做成整体,造型时挖掉妨碍取出模样的那部分型砂,这种造型方法称为挖砂造型。挖
砂造型的分型面为曲面,造型时为了保证顺利起模,必须把砂挖到模样最大截面处(图 6)。
由于是手工挖砂,操作
技术要求高,生产效率低,只适用于单件、小批量生产。
图 6 手轮的挖砂造型的工艺过程
手工制芯
型芯用来形成铸件内部空腔或局部外形。由于型芯的表面被高温金属液包围,长时间受到浮
力作用和高温金属液的烘烤作用;铸件冷却凝固时,砂芯往往会阻碍铸件自由收缩;砂芯清
理也比较困难。因此造芯用的芯砂要比型砂具有更高的强度、透气性、耐高温性、退让性和
溃散性。
手工制芯由于无需制芯设备,工艺装备简单,应用得很普遍。根据砂芯的大小和复杂程度,
手工制芯用芯盒有整体式芯盒、对开式芯盒和可拆式芯盒,如图 7 所示。
图 7 芯盒制芯示意图
零件、模样、芯盒与铸件的关系
模样用来形成铸件的外部轮廓,芯盒用来制作砂芯,形成铸件的内部轮廓。造型时分别用模
样和芯盒制作铸型和型芯。图 1 分别表示零件、模样、芯盒和铸件的关系。制造模样和芯盒
所选用的材料,与铸件大小、生产规模和造型方法有关。单件小批量生产、手工造型时常用
木材制作模样和芯盒,大批量生产、机器造型时常用金属材料(如铝合金、铸铁等)或硬塑
料制作模样和芯盒。
图 零件、模样、芯盒与铸件的关系
铸造铸件常见缺陷分析
铸造工艺过程复杂,影响铸件质量的因素很多,往往由于原材料控制不严,工艺方案不合理,
生产操作不当,管理制度不完善等原因,会使铸件产生各种铸造缺陷。常见的铸件缺陷名称、
特征和产生的原因,见表。
常见铸件缺陷及产生原因
缺陷名称
气孔
特征
产生的主要原因
在铸件内部或表面有大小不等的光滑孔洞
①炉料不干或含氧化物、杂质多;②浇注工具
或炉前添加剂未烘干;③型砂含水过多或起模和修型时刷水过多;④型芯烘干不充分或型芯
通气孔被堵塞;⑤春砂过紧,型砂透气性差;⑥浇注温度过低或浇注速度太快等
缩孔与缩松
缩孔多分布在铸件厚断面处,形状不规则,孔内粗糙 ①铸件结构设计不合理,如壁厚相差
过大,厚壁处未放冒口或冷铁;②浇注系统和冒口的位置不对;③浇注温度太高;④合金化
学成分不合格,收缩率过大,冒口太小或太少
砂眼
在铸件内部或表面有型砂充塞的孔眼
①型砂强度太低或砂型和型芯的紧实度不够,故型
砂被金属液冲入型腔;②合箱时砂型局部损坏;③浇注系统不合理,内浇口方向不对,金属
液冲坏了砂型;④合箱时型腔或浇口内散砂未清理干净
粘砂
铸件表面粗糙,粘有一层砂粒 ①原砂耐火度低或颗粒度太大;②型砂含泥量过高,耐火度
下降;③浇注温度太高;④湿型铸造时型砂中煤粉含量太少;⑤干型铸造时铸型未刷涂斜或
涂料太薄
夹砂
铸件表面产生的金属片状突起物,在金属片状突起物与铸件之间夹有一层型砂
①型砂热
湿拉强度低,型腔表面受热烘烤而膨胀开裂;②砂型局部紧实度过高,水分过多,水分烘干
后型腔表面开裂;③浇注位置选择不当,型腔表面长时间受高温铁水烘烤而膨胀开裂;④浇
注温度过高,浇注速度太慢
错型
铸件沿分型面有相对位置错移 ①模样的上半模和下半模未对准;②合箱时,上下砂箱错位;
③上下砂箱未夹紧或上箱未加足够压铁,浇注时产生错箱
冷隔
铸件上有未完全融合的缝隙或洼坑,其交接处是圆滑的
①浇注温度太低,合金流动性差;
②浇注速度太慢或浇注中有断流;③浇注系统位置开设不当或内浇道横截面积太小;④铸件
壁太薄;⑤直浇道(含浇口杯)高度不够;⑥浇注时金属量不够,型腔未充满
浇不足
铸件未被浇满
裂纹
铸件开裂,开裂处金属表面有氧化膜
①铸件结构设计不合理,壁厚相差太大,冷却不均
匀;②砂型和型芯的退让性差,或春砂过紧;③落砂过早;④浇口位置不当,致使铸件各部
分收缩不均匀
常见铸件缺陷及其预防措施
序 缺陷名称
缺陷特征
预防措施
1
气孔
在铸件内部、表面或近于表面处,有大小不等的光滑孔眼,形状有圆的、长的
及不规则的,有单个的,也有聚集成片的。颜色有白色的或带一层暗色,有时覆有一层氧化
皮。
降低熔炼时流言蜚语金属的吸气量。减少砂型在浇注过程中的发气量,改进铸件结
构,提高砂型和型芯的透气性,使型内气体能顺利排出。
2
缩孔
在铸件厚断面内部、两交界面的内部及厚断面和薄断面交接处的内部或表面,
形状不规则,孔内粗糙不平,晶粒粗大。
壁厚小且均匀的铸件要采用同时凝固,壁厚大
且不均匀的铸件采用由薄向厚的顺序凝固,合理放置冒口的冷铁。
3
缩松
在铸件内部微小而不连贯的缩孔,聚集在一处或多处,晶粒粗大,各晶粒间存
在很小的孔眼,水压试验时渗水。 壁间连接处尽量减小热节,尽量降低浇注温度和浇注速
度。
4
渣气孔 在铸件内部或表面形状不规则的孔眼。孔眼不光滑,里面全部或部分充塞着熔
渣。
提高铁液温度。降低熔渣粘性。提高浇注系统的挡渣能力。增大铸件内圆角。
5
砂 眼
在铸件内部或表面有充塞着型砂的孔眼。
严格控制型砂性能 和造型操作,
合型前注意打扫型腔。
6
热 裂
在铸件上有穿透或不穿透的裂纹(注要是弯曲形的),开裂处金属表皮氧化。
严格控制铁液中的 S、P 含量。铸件壁厚尽量均匀。提高型砂和型芯的退让性。浇冒口
不应阻碍铸件收缩。避免壁厚的突然改变。开型不能过早。不能激冷铸件。
7
8
冷 裂
粘 砂
在铸件上有穿透或不穿透的裂纹(主要是直的),开裂处金属表皮氧化。
在铸件表面上,全部或部分覆盖着一层金属(或金属氧化物)与砂(或涂料)
的混(化)合物或一层烧结构的型砂,致使铸件表面粗糙。
属的浇注温度。提高型砂、芯砂的耐火度。
减少砂粒间隙。适当降低金
9
夹 砂
在铸件表面上,有一层金属瘤状物或片状物,在金属瘤片和铸件之间夹有一层
型砂。 严格控制型砂、芯砂性能。改善浇注系统,使金属液流动平稳。大平面铸件要倾斜
浇注。
10 冷 隔
在铸件上有一种未完全融合的缝隙或洼坑,其交界边缘是圆滑的。 提高浇注
温度和浇注速度。改善浇注系统。浇注时不断流。
11 浇不到 由于金属液未完全充满型腔而产生的铸件缺肉。 提高浇注温度和浇注速度。
不要断流和防止跑火。
铸造铸件金属液的浇注
生产中,浇注时应遵循高温出炉,低温浇注的原则。因为提高金属液的出炉温度有利于夹杂
物的彻底熔化、熔渣上浮,便于清渣和除气,减少铸件的夹渣和气孔缺陷;采用较低的浇注
温度,则有利于降低金属液中的气体溶解度、液态收缩量和高温金属液对型腔表面的烘烤,
避免产生气孔、粘砂和缩孔等缺陷。因此,在保证充满铸型型腔的前提下,尽量采用较低的
浇注温度。
把金属液从浇包注入铸型的操作过程称为浇注。浇注操作不当会引起浇不足、冷隔、气孔、
缩孔和夹渣等铸造缺陷,和造成人身伤害。
为确保铸件质量、提高生产率以及做到安全生产,浇注时应严格遵守下列操作要领:
(1)浇包、浇注工具、炉前处理用的孕育剂、球化剂等使用前必须充分烘干,烘干后才能使
用。
(2)浇注人员必须按要求穿好工作服,并配戴防护眼镜,工作场地应通畅无阻。浇包内的金
属液不宜过满,以免在输送和浇注时溢出伤人。
(3)正确选择浇注速度,即开始时应缓慢浇注,便于对准浇口,减少熔融金属对砂型的冲击
和利于气体排出;随后快速浇注,以防止冷隔;快要浇满前又应缓慢浇注,即遵循慢、快、
慢的原则。
(4)对于液态收缩和凝固收缩比较大的铸件,如中、大型铸钢件,浇注后要及时从浇口或冒
口补浇。
以上就是小编对于铝合金零件铸造过程_铝合金零件铸造过程图片问题和相关问题的解答了,铝合金零件铸造过程_铝合金零件铸造过程图片的问题希望对你有用!
免责声明: 1、文章部分文字与图片来源网络,如有问题请及时联系我们。 2、因编辑需要,文字和图片之间亦无必然联系,仅供参考。涉及转载的所有文章、图片、音频视频文件 等资料,版权归版权所有人所有。 3、本文章内容如无意中侵犯了媒体或个人的知识产权,请联系我们立即删除,联系方式:请邮件发送至 CNC1698@l63.com